Sharing control with robots may make manufacturing safer, more efficient
Hulking robots common to assembly line manufacturing tend to be loners. They often cut, bend and weld metal inside cages and behind barriers meant to safely separate them from human workers.
“For a long time, the best factory robot has been one that you set up, and you don’t touch for two years. It does the same thing over and over, unchanged, a million times,” says Bilge Mutlu, a University of Wisconsin–Madison professor of computer science, industrial engineering and psychology. “But because those robots are built to be very powerful and very accurate, they are also very dangerous for people. You can’t get in its way.”
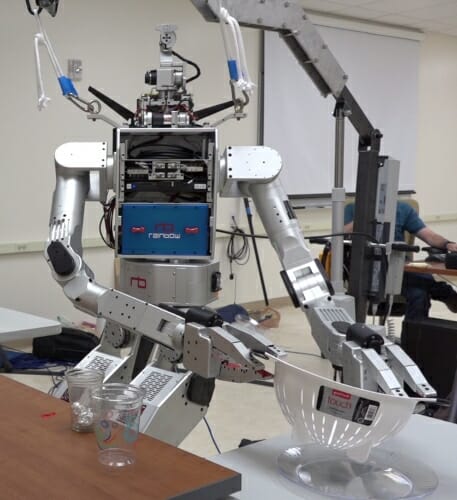
A humanoid robot reaches for a colander at the US Naval Research Laboratory, where UW–Madison researchers and their NRL collaborators have made robots better at working with remote human controllers. Courtesy of Daniel Rakita
With newly won support from NASA, Mutlu and partners at UW–Madison and Boeing are designing lower-power robots that can handle a wider range of less-rigidly defined tasks by working more collaboratively with a human operator.
The UW researchers have focused on “shared control,” in which a human wired with sensors and controls guides a robot’s arms through the course of a task like sorting objects or mixing ingredients according to a recipe. Even new users are able to operate these robots effectively, because the robots step in to help by applying things they’ve been taught about the way humans deftly coordinate the movement of two arms and hands to corral and lift and pass objects.
Mutlu, graduate student Daniel Rakita and computer sciences Professor Michael Gleicher have also published methods for deploying robot-controlled cameras to give the human operator — “whether they’re standing a few feet away or they’re in Houston and the robot is on a space station,” Mutlu says — the best view of the workspace, tools, materials and the robot’s hands.
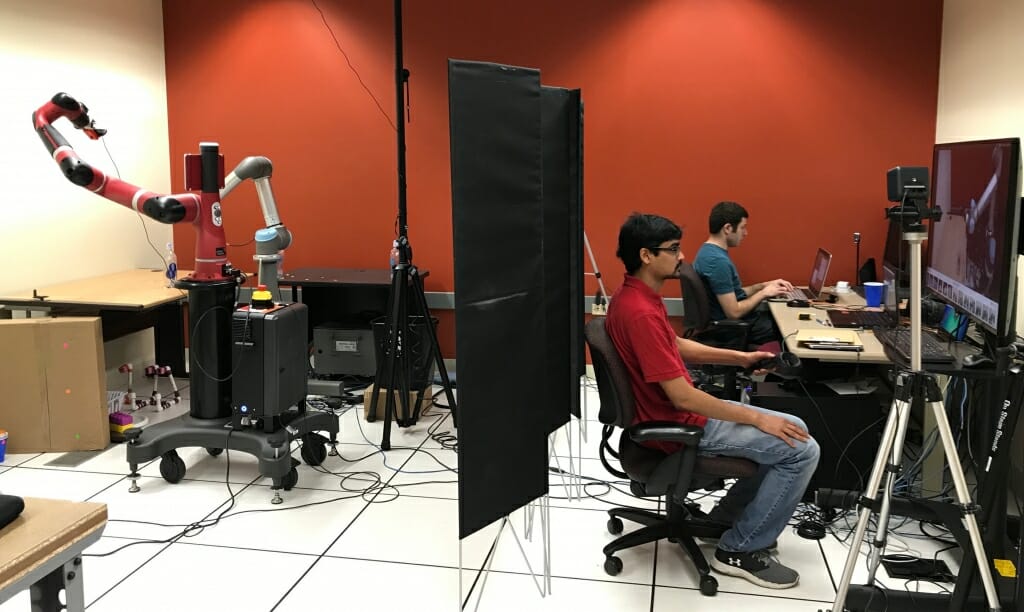
Researchers in UW–Madison’s Collaborative Robotics Laboratory work with a robot arm and camera to manipulate objects. Support from NASA could bring similar systems to work in aeronautics manufacturing. Courtesy of Bilge Mutlu
With that core technology and a $3 million grant from NASA Aeronautics, the UW–Madison group — which includes Gleicher, mechanical engineering Professor Michael Zinn and industrial and systems engineering Professor Robert Radwin — will adapt robots to some of the specific types of manufacturing work that piece together a Boeing airliner.
“We identified a number of processes in aircraft manufacturing where this shared control could help,” Mutlu says. “Take riveting. There are thousands and thousands of rivets that have to be banged in there to join the metal of an airplane together. That’s hard, repetitive work.”
Making composite materials, sanding metal, painting and fitting parts together in confined spaces are other steps in the plane construction process that get safer by moving the relatively fragile human body slightly farther away from the action. Shared control of a robot could make that happen without also removing the human aircraft builder’s skills.
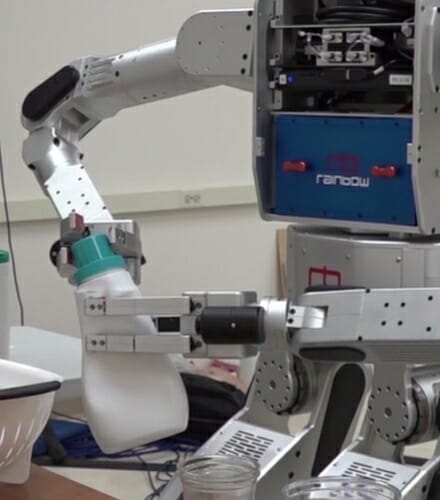
The robot opens a juice container. With “shared control,” a human wired with sensors and controls guides a robot’s arms through the course of a task. Courtesy of Daniel Rakita
“We’re keeping the operator’s expertise, their knowledge of the nuances of the process, in the equation,” Mutlu says. “They can direct the action without being involved manually, and the process gets more ergonomic and efficient.”
Over the next three years, Mutlu hopes the collaboration with Boeing will move a new robot manufacturing platform from Madison to the Boeing laboratories, where it will be further developed for the production floor and then to worldwide use.
“As we’re building it, we’re going to do a lot of testing here in our lab,” he says. “Eventually we want to take it to Boeing and actually demonstrate it there. And a mature, federally funded system that works could be used by anyone in aviation manufacturing.”
Tags: engineering, research