Fitter increases the benefits of wearing a mask during the COVID-19 pandemic
Whether homemade or commercially manufactured, breathable cloth and disposable face masks fit everybody differently, leaving gaps at the top, sides, bottom — or any combination thereof — that could allow virus particles to escape.
Now, a team of University of Wisconsin–Madison engineers has developed a simple and inexpensive do-it-yourself fitter that ensures a tighter mask seal around the wearer’s nose, mouth and face.
Known as the Badger Seal, the mask fitter is a soft, adjustable “frame” with elastic worn either as ear loops or behind the head. With readily available materials, such as elastic cord, foam wire or pipe cleaners, the fitter is easy to make at home in minutes.
When worn over non-medical-grade disposable masks, the Badger Seal significantly improves the masks’ filtration performance, according to research conducted by Scott Sanders and David Rothamer, UW–Madison professors of mechanical engineering and experts in measuring gases and particles in internal combustion engine processes.
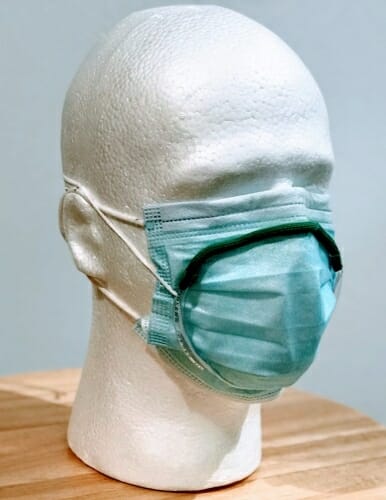
In one version, Badger Seal is an add-on over a mask. It has a single cord around the back of the head and can be worn comfortably for many hours. College of Engineering
The idea for the Badger Seal evolved out of Sanders’ research on the efficacy of face masks. In those tests, Sanders used a mannequin wearing various face coverings — a shield, a homemade four-layer tightly knit mask, and a disposable non-medical-grade filtering mask — to demonstrate how tiny particles from a human breath and larger droplets from a sneeze escape from, or are trapped by, each mask. His results, outlined in a new video, show each mask’s effectiveness at containing both.
During his tests, Sanders also taped the edges of the masks to the mannequin’s face — resulting, unsurprisingly, in the best filtration performance. But while a mannequin might not mind a taped mask seal, Sanders knew he needed a practical solution for people who wanted to “up” the performance of their masks.
He turned to Lennon Rodgers, who specializes in engineering design and directs the Grainger Engineering Design Innovation Laboratory, the engineering makerspace at UW–Madison. During the COVID-19 pandemic, Rodgers pioneered several personal protective equipment, or PPE, solutions now in wide use around the world.
Sanders and Rodgers conducted an initial web search that yielded a few mask fitter solutions using rubber bands, 3D-prints and more custom designs. None of the designs they found seemed viable for widespread adoption due to their cost, comfort and adjustability.
Rodgers made a quick online order of a dozen or so different candidate materials, then embarked on an iterative engineering design and prototyping process. As he refined each mask fitter prototype, Sanders and Rothamer tested it until the team arrived at a Badger Seal that is both effective and comfortable to wear.
“Adding the Badger Seal to a three-ply disposable mask helps contain aerosols and droplets,” says Sanders. “For wearers, a sign of a tight fit is when the mask material moves in and out with each breath.”
Makerspace staff and students have made approximately 2,500 fitters in-house — many of which have been distributed to specific UW–Madison faculty and staff, including overnight employees charged with deep-cleaning some university residence halls.
“They are used in a place where they already would wear a disposable mask,” says Mike Kinderman, director of residence hall facilities in the Division of University Housing. “From people on the night shift, the comment is that they do work. It’s like one of those inventions that you look at afterward and think, ‘Someone figured out a way to hold a mask tighter to your face. Why didn’t I invent this?’”
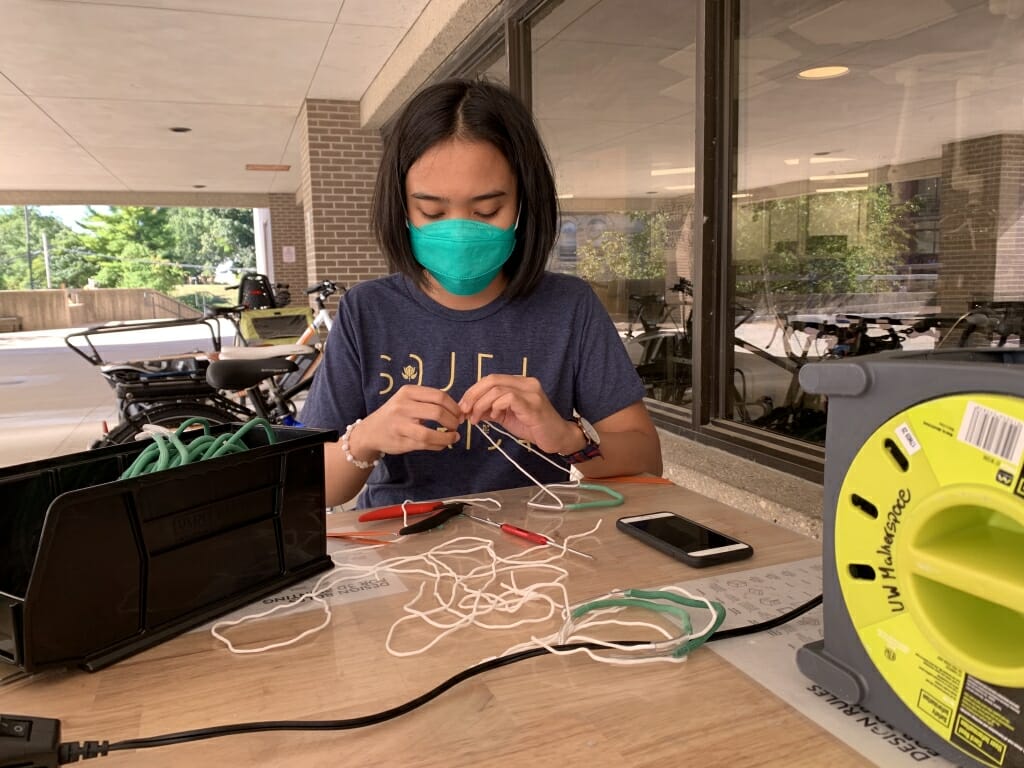
In early fall 2020, College of Engineering student employees assembled Badger Seal mask fitters outside the Grainger Engineering Design Innovation Laboratory in Wendt Commons. Renee Meiller, UW–Madison College of Engineering
Rodgers says he hopes a company will pick up the Badger Seal design and manufacture it commercially. However, it’s also easy to make at home using the open-source design posted on the Badger Seal website. There also is a make-your-own station for members of the UW–Madison community in the makerspace lobby.
Michael Arnold, a UW–Madison professor of materials science and engineering, teaches a materials experience course for first-year students. This semester, their first hands-on activity was to use the how-to video to make a Badger Seal.
“What a perfect opportunity to expose freshmen on their very first day to Wisconsin engineering, and to show them right off the bat how engineers can solve problems to make society a better place,” he says.
The Badger Seal is a good mask addition for people in many public-facing sectors across the country, Sanders says. He even shared the how-to video with his mom: “She has some teacher friends who wanted to make the fitters to enhance their masks.”
Arnold has also received positive feedback from his students, many of whom started wearing the Badger Seal regularly. “If such a simple measure as making and wearing a mask fitter can make masks work better, and at very little cost or hassle to the wearer, then why wouldn’t everyone want to wear one?” he says.
Enjoy this story?
Read more news from the College of EngineeringTags: College of Engineering, covid-19, health, materials, UW impact